OUR BUSINESS
Five Principles of MATSUOKA
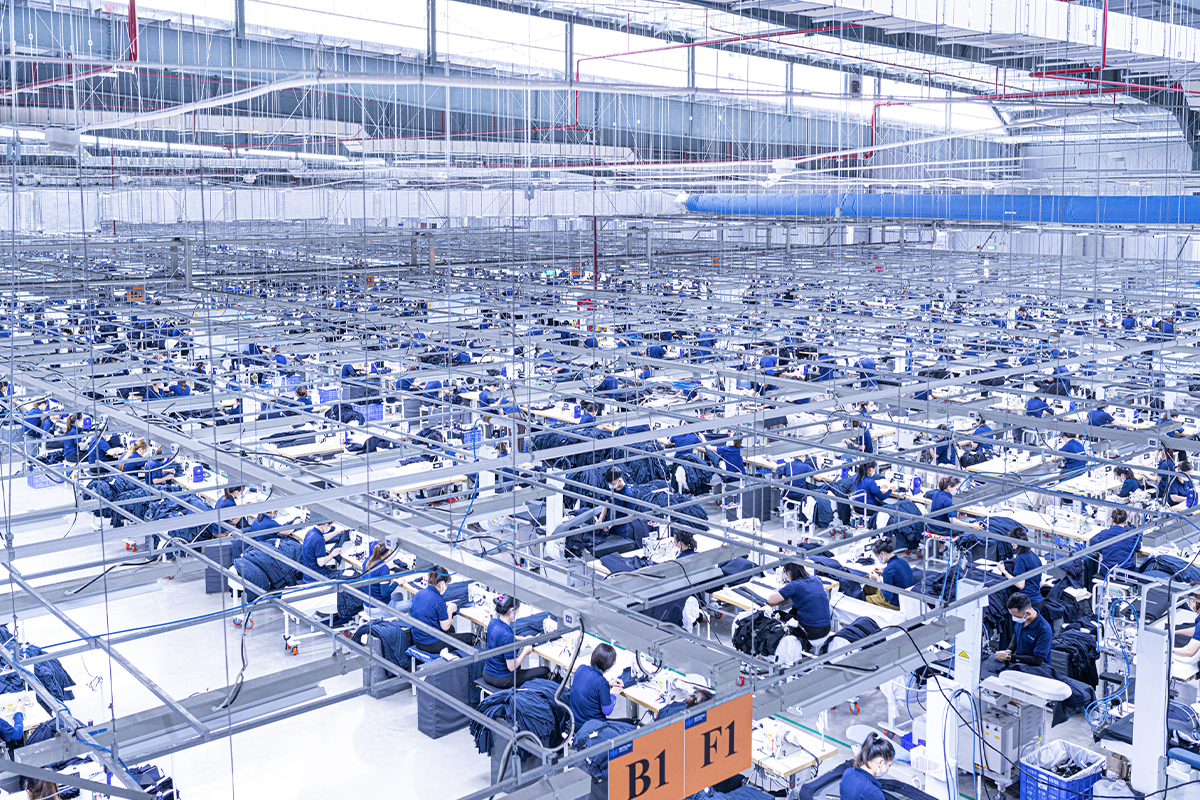
Five Principles MATSUOKA’s business
The apparel industry continues to grow on a global scale with greater speed. Moreover, investments in equipment that reduces environmental loads and also quality of life improvements regarding working environments have come to be valued in recent years. We are always evolving our manufacturing in line with the needs and changes of the times. In order to maximize improvements in productivity and realize stable quality standards, we place importance on five points.
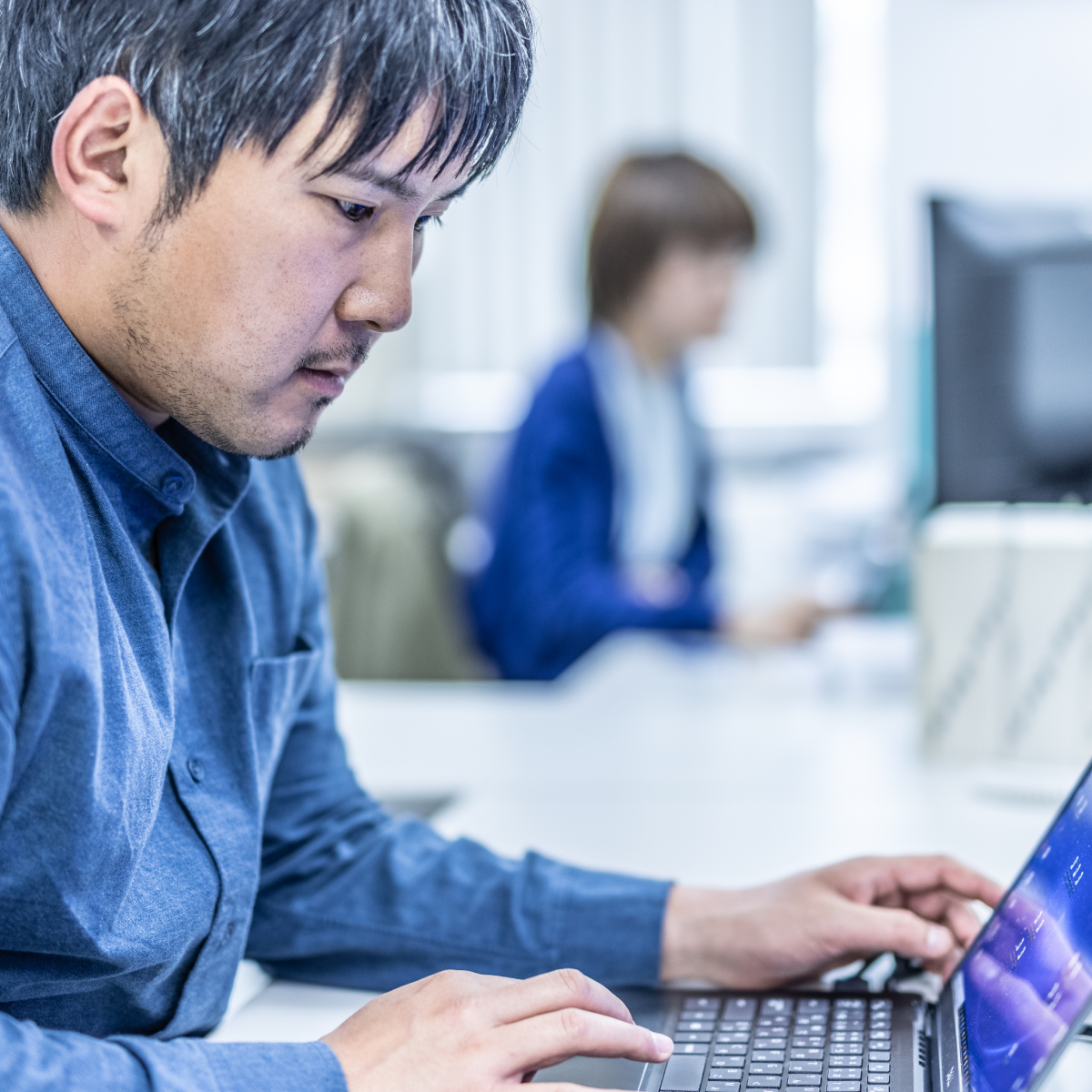
Point 1
Thorough preparations on the assumption of mass production
At the time of making samples, we select a factory according to product characteristics, and clarify possible problems in mass production from the perspective of the production site. After thoroughly understanding the order details, we organize information by breaking it down and processing it into information that is easy to convey to the factory. Global information transmission, including daily communication and document translation, enables information sharing and reducing the risk of mistakes. Due to our management system that allows us to directly communicate with the factory, we are able to create an environment in which the factory can concentrate on their production.
- Accurately conveying the order details and detailed specifications through Japanese points of view
- Selecting a factory that meets the order details, so that it can be put into practice in the country of production
- Translating the written instructions and order details in Japanese and the local language, and building a structure in which the details can be checked for inconsistencies
- Capable of adjusting the instructions in design, etc., to industrial patterns for factory production
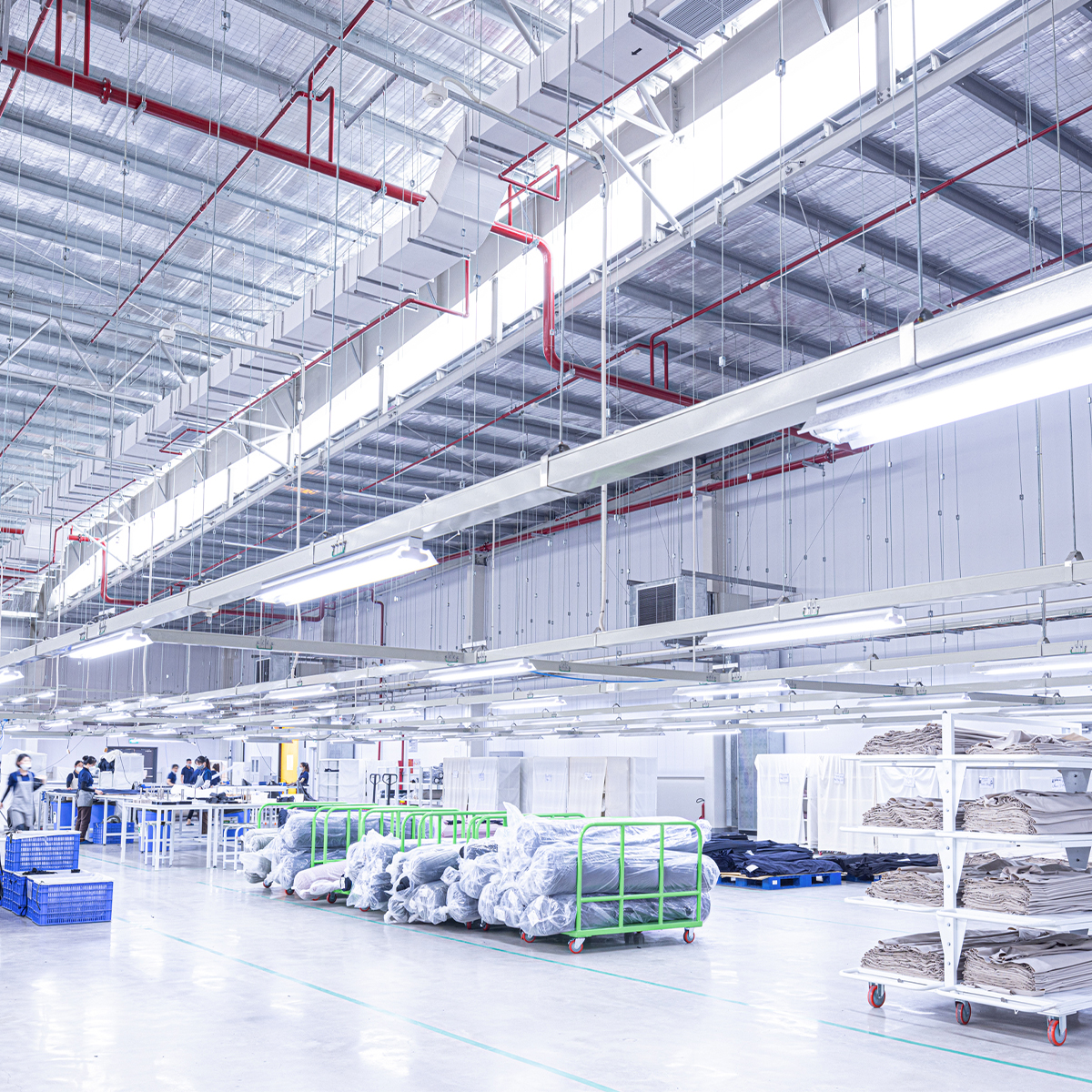
Point 2
Elaborate production management through a full understanding of field sites
In order to deliver high-quality products by the delivery date, we constantly trace the status of all materials based on: Where are the fabrics? When will buttons, zippers, and quality labels arrive at the factory? In addition, to secure production lines according to orders, we share linked information between our factories around the world and the Head Office, including order forecasts, production capacity, material arrangement status, and quality check result reports.
- Responding and adjusting capabilities to realize centralized management of planned production through delivery date
- Confirming the production capacity, material quality checks, and situations up to the delivery date at weekly meetings
- Avoidance of conflicts, disasters, and other risks in the country of production through operation of factories in various countries
- Cross-border exchange of funds and handling of money orders, and ensuring of abundant purchase funds
- Visualizing the progress of sales activities and forecasts for orders received, and sharing them between all factories
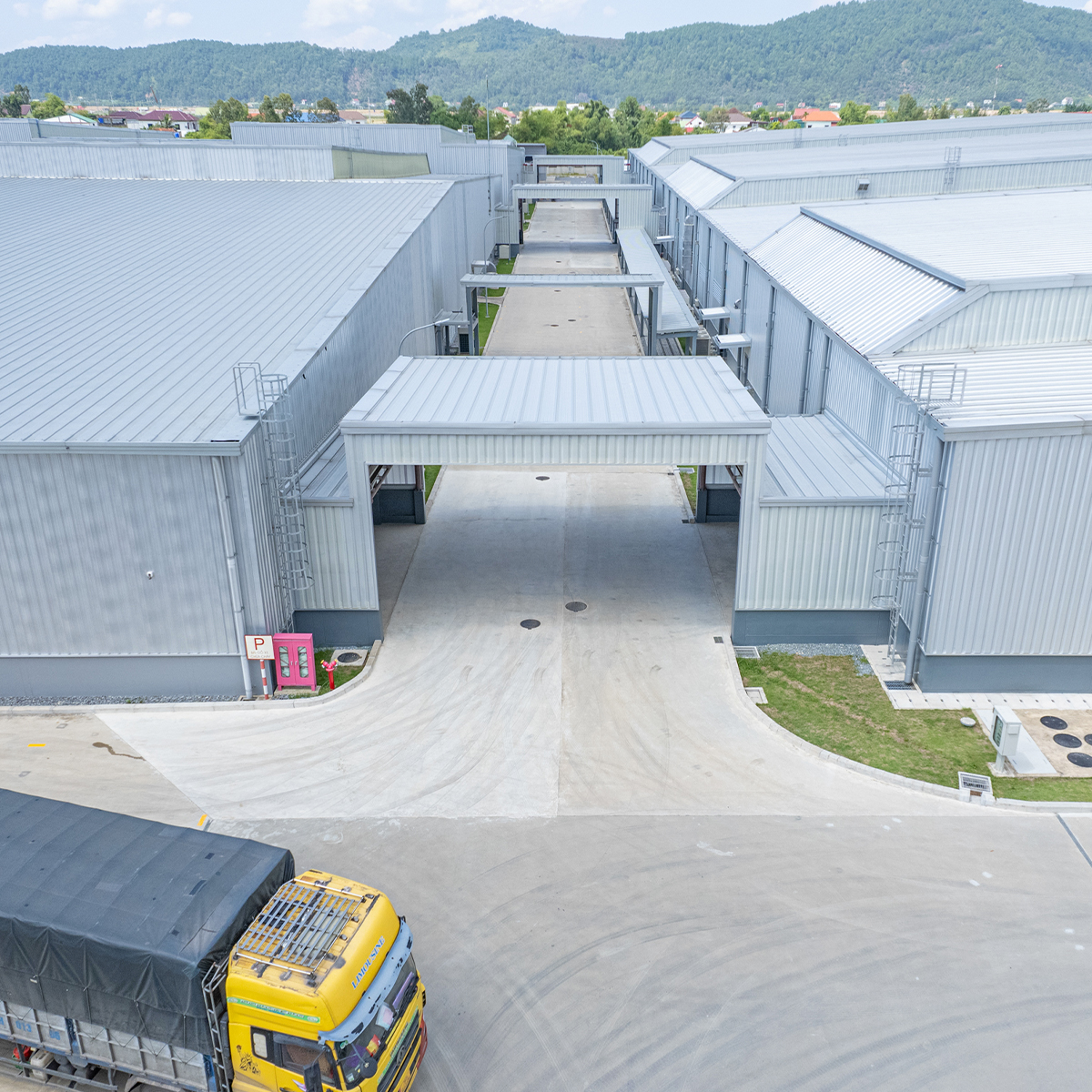
Point 3
Unique structure for total management of trade and logistics
Even if good products are made, it is meaningless unless they are delivered to a designated place by the delivery date. We realize safe transportation at reasonable costs not only by constantly tracing the conditions of products having been shipped from our production site but also by arranging shipping service ourselves. We also visualize the status of marine transportation, etc., in real time, and share it with our customers. We are ready to cooperate immediately and propose optimum solutions even in the event of the occurrence of any risk.
- Seamless status confirmation by our unique management system
- Centralized management of information for all materials and products at the Head Office
- Avoidance of problems by thorough schedule management and quick response at the time of occurrence of problems
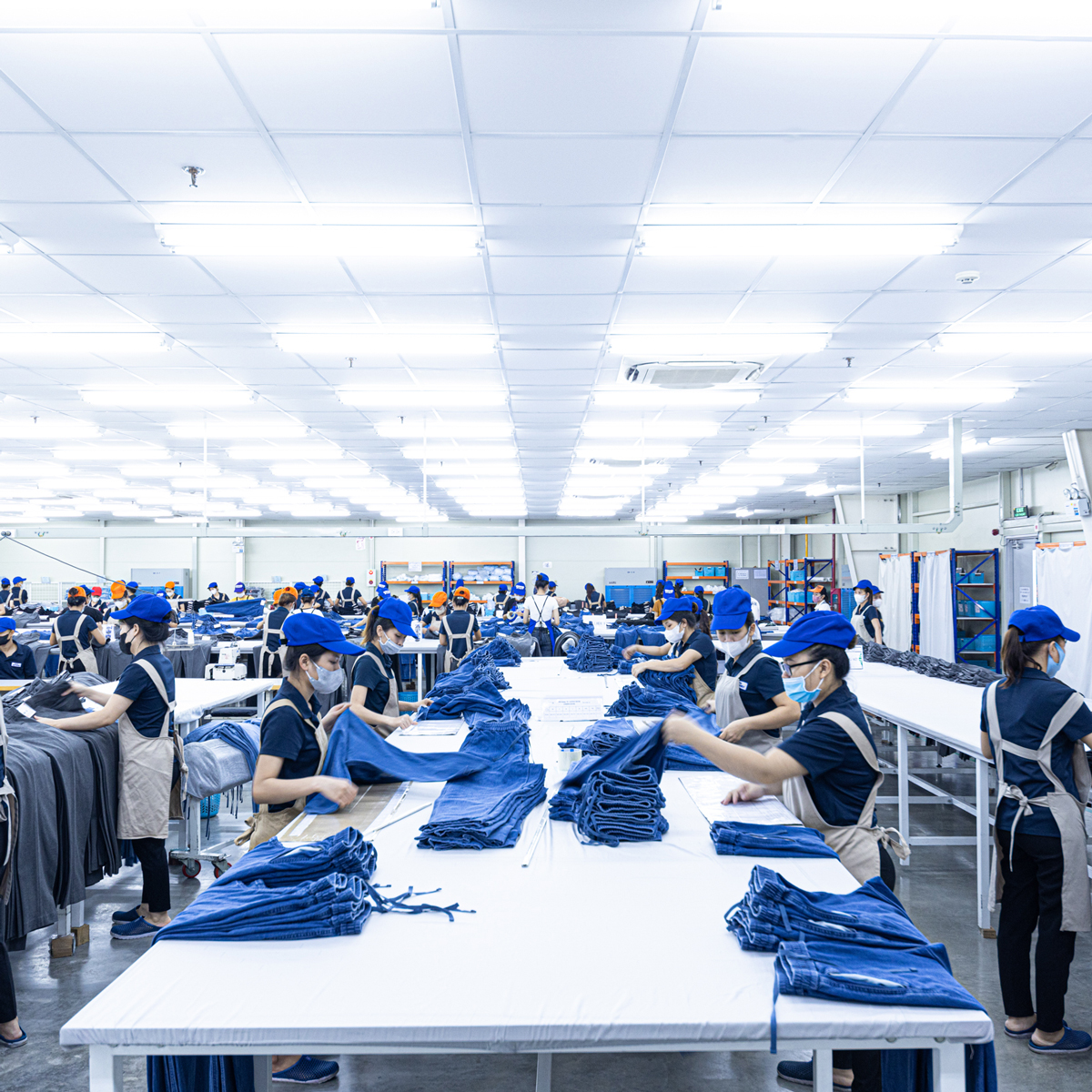
Point 4
Thorough quality control
For realization of environments that reassure our customers, we believe it is important to create environments in which our factories can concentrate on high-quality manufacturing. By managing information thoroughly, we have created such environments globally. One of them is “OTM (One Table Meeting)” in which relevant parties from the field site and the Head Office are seated around one table before input of materials. In addition, we ensure high quality by performing material quality inspection before production and 100% inspection before delivery. All the number of defectives and their causes are recorded and retained. We never run from our responsibility. That is MATSUOKA’s manufacturing.
- OTM (One Table Meeting) at the time of quality inspection or before input of materials
- Confirmation of the mass production system at a “briefing” after material input into production line (remote)
- Capability to investigate causes and solve problems at the time of occurrence of defectives
- Implementation of 100% inspection before shipping products and sampling inspection by third-party organizations
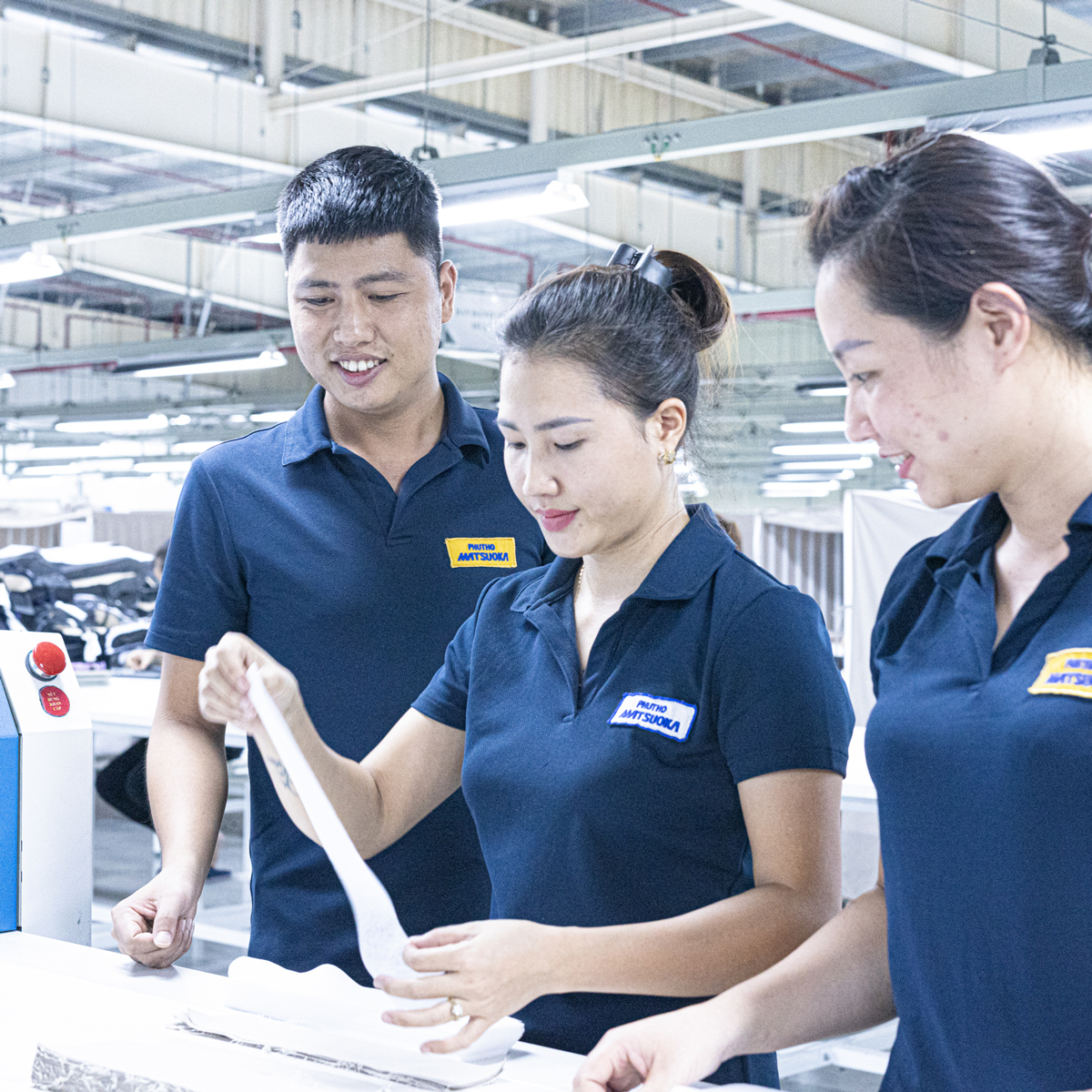
Point 5
Education system to develop managers and localize Japan-based work
In order to develop managers who can provide proper education, staff working at local factories are educated in Japan. Our multi-year training program is intended to deepen levels of understanding of our thoughts on work and improvements, and share awareness in terms of quality and management, focusing on learning the Japanese language. By developing good managers, we will enhance the reproducibility of work and education, and provide stable work through global supply chains.
- Training of trainees from each factory in Japan
- Training programs according to career ladders
- Creation of education manuals in each local language